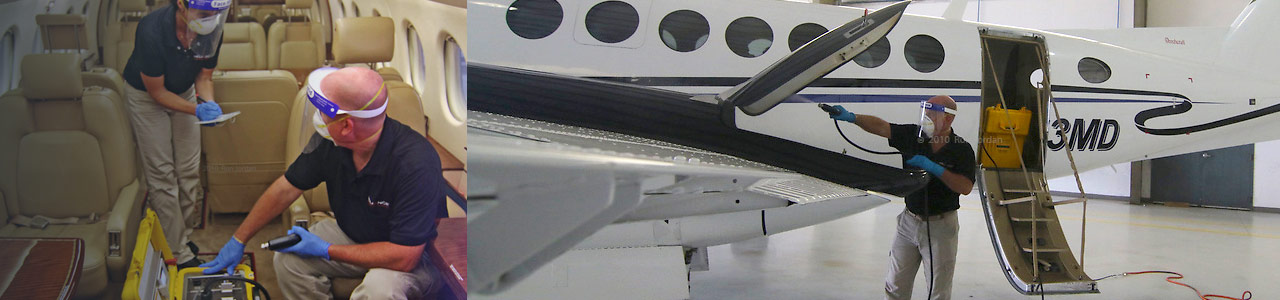
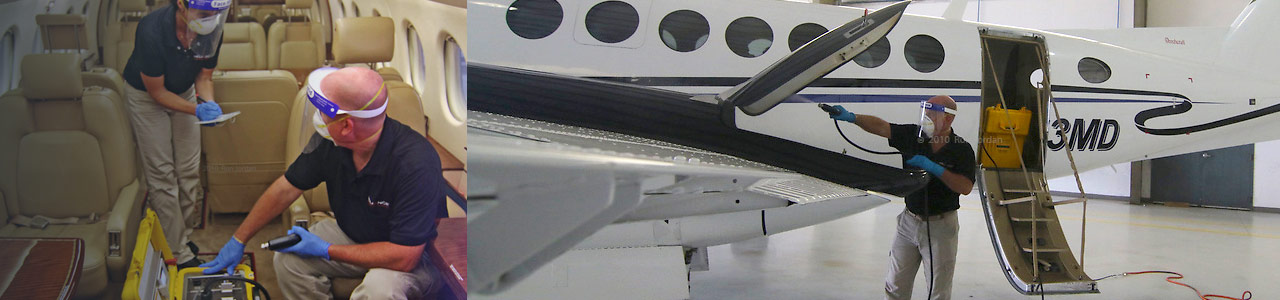
You probably have questions and, thankfully, we have the answers. Here is everything you need to know about our disinfection process, cleaning solution, what you can expect when doing business with us, and much more.
Still have a few more questions about our services? Complete our Request a Quote page, and someone will be in touch with you as soon as possible.
We use the AeroClave RDS 3110 decontamination system. The RDS 3110 is a rugged, lightweight and portable decontamination system that can effectively treat spaces up to 5,000 cubic feet. Larger aircraft can be treated with multiple units. The machine provides the ability to aerosolize our Boeing-tested, EPA-approved disinfection that produces no harmful by-products for the environment, contains no VOC’s and is 100% biodegradable.
AeroClave was chosen to decontaminate the Florida Infectious Disease Transportation Network. Learn why.
Here are two independent lab studies that evaluated the potential for damage of aircraft materials and surfaces as a result of use of Vital Oxide with positive results that you may download below.
Vital Oxide has been approved by the EPA for use against SARS-CoV-2, the coronavirus that causes coronavirus disease 2019 (COVID-19). It meets the EPA’s emerging pathogen requirements for viruses showing efficacy against envelop and non-envelope viruses, both large and small.
There is generally no discernible residue left behind. However, depending on conditions, it is possible for the disinfectant solution to leave a light residue behind similar to hard water spotting. If this happens, as part of our process, we will wipe down affected glossy surfaces to remove this residue.
The disinfectant we use is an EPA-registered hospital disinfectant cleaner, mold and mildew killer, and odor eliminator. It is gentle to users, but tough on germs. It is non-irritating to skin, non-corrosive to most treated surfaces, NSF-certified (no rinse required) for food contact surfaces, and listed as a category IV (lowest toxicity category) pesticide with the EPA.
“No rinse required for food contact surfaces” is a safety rating given by NSF International (previously the National Sanitation Foundation). The NSF testing guidelines are a continuation of the USDA product approval and listing program, including the FDA 21. Vital Oxide is rated “no rinse required on food contact surfaces” category D2, meaning Vital Oxide is approved for use in commercial or residential kitchens to control bacteria, viruses, and mold without the need to wash/rinse the area with water after Vital Oxide is applied.
There are no lasting insecticidal effects after the process is completed and the solution has dried. We know of no safe and appropriately approved substance that has such capabilities. Anyone making claims otherwise about other products are likely using a very caustic, damaging or dangerous product, or are greatly mistaken about the lasting capabilities of their product.
Employing an aerosolized disinfectant solution inside the cabin treats all exposed interior cabin surfaces without regard to linear lamp limits or cabin obstructions. This means that areas of the cabin that are not properly exposed during UV light treatment because of UV light coverage limitations or obstruction shadowing, are exposed to our aerosolized fog solution. Additionally, repeated exposure to concentrated UV light causes significant damage to many materials.
There are some circumstances in which spraying is appropriate for decontamination, such as when treating checked luggage bins where the goal is to apply solution to a simple surface area. However, in more complex environments containing irregular physical profiles and in larger expanses, manual application can miss significant areas. Filling the entire cabin with aerosolized disinfectant leaves little question about how consistent the coverage is.
This depends on several factors. Individual aircraft operators should develop their own best practices in this regard based on their situation. We will be pleased to assist you and evaluate your options.
Request a Quote today to discuss your needs with a sales representative.
Yes. You will be provided with a pre-arrival checklist that provides guidance for preparing the aircraft and choosing an appropriate area for the operation. At a minimum, we will require access to 110VAC 60 Hertz (15 amp minimum) power outlet near the aircraft.
The process typically takes about one hour, or less, for aircraft up to 5000 cubic feet of total cabin volume.
Reliance Aerotech Services (RAS) has been in business providing aircraft maintenance and servicing operations for more than 20 years. We have performed in numerous states and countries in all sectors of aviation.
Our Aircraft Disinfection Technicians are experienced Aircraft Maintenance Technicians who have gained their Institute of Inspection Cleaning and Restoration Certification (IICRC) Health and Safety Technician Certificate. This certification requires mastery of related OSHA standards, Inspections, Citations and Penalties, Record keeping, Personal Protective Equipment (PPE), Hazard Communication, Hazardous Materials, Confined Spaces, and Bloodborne Pathogens.
Our technicians are also trained on the RDS 3110 aircraft disinfection procedure.
We have strategically located this capability regionally throughout the USA and Canada. Please contact us to see if we have a technician nearby or to arrange for deployment of the capability to an overseas location.